View previous topic :: View next topic |
Author |
Message |
tomigv Member
Joined: 11 Apr 2008 Posts: 50 Location: lee/s summit mo
|
Posted: Mon Apr 14, 2008 9:50 am Post subject: art/hobby store varnish |
|
|
Hi I was at a hobby/art shop and noticed quite a number of different types of art varnish,They had names such as copal, dammar, etc and stand oil, etc . Has anyone used these for finishing violin family instruments??. Or is it safer to buy a commercial type varnish thanks ernie?? _________________ I am very interested in violin and bow making. Have quite a few interesting bows and a large cache of pernambuco. I like to experiment using local midwest hardwoods, |
|
Back to top |
|
 |
MANFIO Super Member
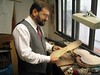
Joined: 11 Apr 2007 Posts: 458 Location: Sao Paulo
|
Posted: Mon Apr 14, 2008 10:20 am Post subject: |
|
|
Good violin varnish is a bit different than the commercial things you will find in commerce.
There are some ready made varnishes being produced now, I'm currently using Magister Products varnishes with good results. They have a website. _________________ www.manfio.com
http://www.flickr.com/photos/7875988@N02/with/464604020/ |
|
Back to top |
|
 |
Andres Sender Super Member
Joined: 23 Mar 2007 Posts: 275 Location: N. CA
|
Posted: Mon Apr 14, 2008 2:50 pm Post subject: |
|
|
Artist’s varnishes are formulated with different goals in mind than violin varnishes. Most if not all of them are specifically intended to be reversible.
A very basic commercial hardware store varnish which has only oil and either phenolic or alkyd resin in it can probably make a serviceable violin varnish, although I understand that the optical properties may not be ideal. For a first instrument that may not be much of an issue. If I were going down that road I would look at non-polyurethane spar varnishes or the Behlen Rock Hard Tabletop varnish which I have heard mentioned on several occasions. Since ‘rock-hard’ doesn’t sound like the greatest idea for a violin varnish I’d consider experimenting with adding some oil to the latter formula. |
|
Back to top |
|
 |
actonern Super Member
Joined: 15 Aug 2007 Posts: 444
|
Posted: Mon Apr 14, 2008 3:57 pm Post subject: |
|
|
tomigv:
You really should consider trying to make your own varnish. The reason is the same as that which tempts many of us to make instruments ourselves, rather than buy one of the many very good ones already available for ready purchase...
You'll need at a minimum space outside that allows you to cook the varnish... the stuff smells very nasty and would be impossible to do inside the house... the possibility (very controllable) of fire also makes outside cooking mandatory.
Get an electric hot plate and a candy thermometer that allows temperature readings at the high end of 500 degrees F or so.
The recipies are legion; my latest has been applied to a cello and I'm really happy with it.
Add an equal weight of Pine rosin (Greek pitch or Colophony is how its referred to in many ancient scripts) and mastic ( I used 200 gms mastic and 200 gms rosin in my last batch) to a cheap disposable non-iron containing pot and start to melt the contents on medium heat (about 450 degrees). It will slowly begin to melt and then begin to froth up in the pot. This is called the "exothermic" reaction and it must be watched carefully at this point as the volume can rise many times the original... the pot should be chosen for a size capable of handling this "frothing" action, or about 5 times the original volume. When it froths up too much take it off the heat till it subsides again. After about 1/2 hour the mass will reduce back to a clear resinous liquid. Keep it on the heat, at about 450 degrees, or at a gentle rolling boil.
The time thus spent cooking the resin is subject to choice. If you cook it long it will reduce in mass, and become darker. Even at it's darkest, (say for example cooked thus for 6 hours or so) it will still not be dark enough to varnish an instrument without the addition of extra colorants, so it's pointless to cook too long.
When the resins are have cooked as long as you like, take the pot and weigh it with resins inside. subtracting the weight of the pot, add an equal weight (as the remaining resin) of unprocessed raw linseed or walnut oil to the mix. The oil should be pre-heated up to roughly the temperature of the resins before mixing in. This can be done inside on your stove top.
Raise the heat again to 500 degrees and cook some more. Some authorities will cook for little time, say 1/2 hour more, but I like to keep going till a small drop of this cooking varnish applied to the back of a spoon can be "pulled apart" into an unbroken strand between spoon and finger. This may take several more hours, but doing so I've found is a useful way to get the varnish to dry faster when applied to your instrument.
When you've reached this stage the varnish is done. You may choose then to add a bit of turpentine, or not, and add thinning agents later.
This varnish can be cooled, bottled and will last for years.
It is absolutely necessary that when applied the varnish be exposed to UV rays of sunlight or UV lamps or it won't dry at all. Thus exposed, however, it will dry to the touch in a few hours and can be recoated in a day or so.
What I like about this varnish is that it's quite naturally glossy and has the quality of self "healing"... small scratches such as you would get from sanding the top coat with micromesh just disappear on their own...
I have to credit "Manfio" for all his help in getting brave enough to try making varnish myself, and wouldn't presume to claim any special insights into the process, but I can say that this recipe will make a very good varnish.
Best regards, |
|
Back to top |
|
 |
M_A_T_T Member

Joined: 03 Apr 2007 Posts: 43
|
Posted: Tue Apr 15, 2008 12:33 am Post subject: |
|
|
I've been experimenting with Dammer resin, Mild Citrus thinner/solvent, Stand oil, linseed oil, walnut oil, etc. Dammer, dissolved in a Citrus solvent, with Walnut Alkyd Meduim, along with a color is what I've been testing. Coloring with Windsor Newton art store paints yields a finish that never fully cures, coloring with raw asphalt seems to work if you don't add to much, but I don't really like the color. At the same time I am testing some commercial Joseph Hammerl JOHA 1A Oil Varnish and the results are FAR better. _________________ Making a Violin II
Making a Violin III - Finally Finished |
|
Back to top |
|
 |
tomigv Member
Joined: 11 Apr 2008 Posts: 50 Location: lee/s summit mo
|
Posted: Tue Apr 15, 2008 9:24 am Post subject: hobby store varnish |
|
|
Thanks to all of you, for your suggestions. I tried to make a small batch of varnish using linseed oil, rosin, and turpentine. It wound up on a ukulele and looked good. I also have 3 bottles of hidersine spirit varnish, which i presume can be thinned with alcohol. I can spray them with a gun if thinned enough. I will check into commercial varnishes as well. It seems there is no one answer. But which method works best for you. and gets the results your after.Thanks to all who shared ernie _________________ I am very interested in violin and bow making. Have quite a few interesting bows and a large cache of pernambuco. I like to experiment using local midwest hardwoods, |
|
Back to top |
|
 |
shershey Member
Joined: 26 Mar 2007 Posts: 28 Location: Dillsburg, PA
|
Posted: Fri Apr 25, 2008 10:40 am Post subject: Varnish |
|
|
Tom, you may want to look into this DVD on spirit varnishing "How to Spirit Varnish" by Scott W. Hershey. It includes recipes as well, see details @ hersheyviolins.com or Stewart McDonalds. they also carry the DVD. Good luck, Scott W. Hershey |
|
Back to top |
|
 |
arglebargle Junior Member
Joined: 11 Feb 2008 Posts: 5 Location: Brunswick, Maine
|
Posted: Fri Apr 25, 2008 1:24 pm Post subject: |
|
|
Not that you would have any interest in the transaction.
 |
|
Back to top |
|
 |
|
|
You cannot post new topics in this forum You cannot reply to topics in this forum You cannot edit your posts in this forum You cannot delete your posts in this forum You cannot vote in polls in this forum
|
Powered by phpBB © 2001, 2005 phpBB Group
|